silicon carbide crucible
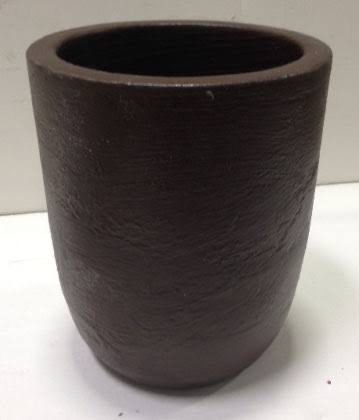
Designers create the graphite Silicon carbide crucible mold for silver to hold molten silver, gold, or other precious metals, shaping them into desired forms. Composed of 99.9% pure graphite with less than 0.1% ash content, this mold ensures that precious metals remain uncontaminated.
This graphite mold is versatile and suitable for a variety of applications, including holding molten gold, silver, or other metals. It is ideal for both testing and ingot casting.
With excellent thermal stability, the mold supports rapid cooling and offers robust corrosion resistance against acids and alkalis. Its superior thermal conductivity significantly reduces casting time and conserves energy. The mold maintains its original physical and chemical properties of natural graphite.
Some manufacturers design graphite molds for silver to cast multiple bars simultaneously, which enhances both speed and quality in the casting process.
- parameters
- features & benefits
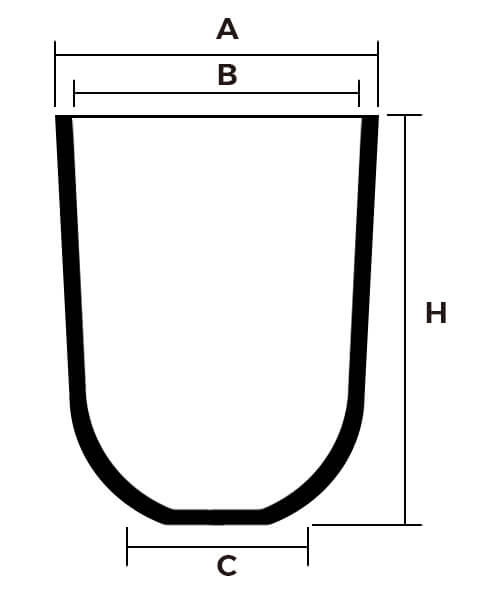
Model | A ± 5mm | B ± 5mm | C ± 10mm | H ± 10mm |
scc 26 | 170 | 130 | 115 | 220 |
scc 28 | 170 | 130 | 115 | 260 |
scc 30 | 205 | 162 | 130 | 265 |
scc 40 | 240 | 200 | 170 | 335 |
scc 60 | 270 | 210 | 180 | 335 |
scc 85 | 295 | 240 | 225 | 400 |
scc 90 | 305 | 248 | 150 | 345 |
scc 95 | 310 | 255 | 170 | 345 |
scc 100 | 310 | 240 | 220 | 350 |
scc 110 | 325 | 266 | 205 | 380 |
scc 153 | 375 | 310 | 200 | 400 |
scc 154 | 395 | 325 | 220 | 580 |
scc 155 | 390 | 330 | 220 | 650 |
scc 170 | 355 | 295 | 280 | 480 |
scc 200 | 400 | 349 | 215 | 510 |
scc 201a | 420 | 360 | 215 | 505 |
scc 202 | 425 | 350 | 230 | 530 |
scc 203 | 430 | 355 | 230 | 600 |
scc 204 THIN | 420 | 360 | 210 | 500 |
scc 205 | 430 | 360 | 230 | 650 |
scc 292 | 510 | 444 | 290 | 450 |
scc 293 | 500 | 444 | 290 | 510 |
scc 300 | 450 | 390 | 250 | 500 |
- Industries widely use graphite molds for silver in aluminum, gold, and silver casting due to their superior quality, which makes them ideal for intricate mold designs and high-volume production runs.
- Graphite molds for silver remain highly stable and do not twist or crack when you pour molten metal into them. Even with constant use, the molds remain durable and do not deteriorate. However, it is important to note that a graphite mold for silver has a relatively limited life expectancy.
- The graphite mold for silver offers exceptional thermal conductivity, even under sudden temperature fluctuations. It also boasts excellent oxidation and corrosion resistance, making it ideal for refining purposes.
- Metals cast using the graphite mold for silver remain pure because the mold prevents exposure to impurities and contamination.
- The smooth finish of the mold’s cavity ensures that cast metals are easily removable and do not stick once cooled.
- Volcano Corporation crafts its graphite mold for silver from high-quality graphite with a fine particle structure and a high degree of graphitization. This composition results in a dense mold structure, minimizing porosity, while also providing a smooth surface and a low rate of heat deformation. Additionally, the mold exhibits high mechanical strength, with tensile strength increasing at elevated temperatures compared to other materials.
- Volcano Corporation’s graphite mold for silver offers exceptional thermal shock resistance, making it suitable for various processes. It also features excellent thermal conductivity and strong oxidation resistance.
- To prevent cast metal from adhering to the mold surface, the graphite material exhibits minimal adhesion to the solidified metal.The mold’s low wettability with liquid metal ensures easy removal of the casting.
- The graphite mold for silver offers self-lubricating properties. Its low friction between the mold surface and the solidified metal ensures smooth removal of the casting, preventing cracks and reducing the thickness of any defective surface.
- The graphite mold for silver casting is easily machinable using graphite. Techniques such as milling, grinding, and turning enable the creation of molds with a fine surface finish, complex shapes, and tight tolerances. We finish the inner surface of the mold to minimize wetting and friction with the cast material, ensuring a smooth casting process.